Plant Manager
Northern Steel Ltd
9588 Milwaukee Way Prince George British ColumbiaDescription
The Plant Manager is accountable for the overall operational efficiency of the plant, ensuring a safe, productive, and high-quality fabrication environment. This role prioritizes Health, Safety, and Environmental (HSE) compliance, leveraging the HSE department to uphold and enforce safety standards. The Plant Manager drives productivity through data-driven decision-making and ongoing assessments of the workforce and operational performance.
This position develops and executes shop production strategies derived from project execution plans, balancing cost, quality, and schedule targets. With HR accountability and experience managing a unionized workforce, the Plant Manager fosters a culture of continuous improvement while recruiting, retaining, and developing a high-performing team.
Entrepreneurial in approach, the Plant Manager identifies and implements production efficiencies and cost-saving opportunities, always maintaining a cost-conscious mindset. This role is responsible for aligning Safety, Quality, and Production priorities to meet business objectives while ensuring compliance with all operational, legal, and contractual requirements.
Duties
Production Management
- Develop and maintain a production schedule
- Oversee all fabrication and machining operations to optimize efficiency and meet or exceed project budget hours.
- Organize and assign work received from the Project/Estimating department, ensuring proper execution by foremen and production staff.
- Monitor and adjust manpower usage daily to maintain project schedule and production goals.
- Lead production coordination to meet key customer deadlines and internal quality standards.
- Develop execution plans that maximize material handling efficiency and minimize handling time for goods and materials.
Health, Safety, and Environmental (HSE) Accountability
- Champion HSE initiatives and ensure strict compliance with all relevant safety regulations, standards, and procedures.
- Address unsafe actions or conditions immediately and document corrective measures.
- Conduct safety audits and inspections, implementing recommendations and ensuring follow-up.
- Investigate incidents and near misses, identify root causes and implement corrective actions.
- Collaborate with the HSE team to develop, promote, and enforce safety training programs.
- Maintain accurate records of HSE activities and ensure adherence to the company’s return-to-work policy for injured employees.
Leadership and Supervision
- Directly supervise foremen, charge hands, and production crews, ensuring alignment with company objectives.
- Conduct regular employee reviews to assess performance, set goals, and address training needs.
- Lead and document progressive discipline for underperforming employees in line with company policies.
- Build a collaborative, high-performance team culture that promotes accountability, safety, and efficiency.
Process and Quality Improvement
- Review systems, processes, and equipment to identify and implement improvements that enhance production efficiency and profitability.
- Contribute to ISO 9001 quality program compliance by ensuring adherence to documented procedures and standards.
- Analyze production data and recommend changes to improve workflow, reduce waste, and increase output.
Collaboration and Communication
- Act as a liaison between production, project managers, quality assurance, material coordinators, and other departments to ensure seamless coordination.
- Attend project kickoff meetings and provide ongoing updates on progress, manpower, and resource needs.
- Provide timely feedback to the General Manager on production issues, challenges, and opportunities.
Qualifications
Education and Experience
- High School Diploma or equivalent required.
- Trade certification in a related field (e.g., Welding, Metal Fabricator (Fitter), Machinist) is an asset.
- Minimum 10+ years of experience in steel fabrication or machining operations.
- At least 5 years of supervisory experience in a manufacturing or fabrication environment.
Skills and Competencies
- Strong knowledge of manufacturing, steel fabrication processes, and ISO 9001 quality requirements.
- Ability to read and interpret technical drawings, specifications, and project documents.
- Exceptional leadership, team-building, and interpersonal skills.
- Proficient in production planning, process improvement, and time management.
- Demonstrated expertise in HSE compliance and implementation of safety programs.
- Skilled in conflict resolution, employee motivation, and performance management.
- Competency with Microsoft Office (Word, Excel, Outlook) and production scheduling software.
Work Environment
- Heavy industrial environment with exposure to noise, dust, fumes, and extreme temperatures.
- Compliance with proper use of personal protective equipment (PPE) is mandatory.
Benefits
- Company pension
- Dental care
- Disability insurance
- Extended healthcare
- Life insurance
- Paid time off
About The Company
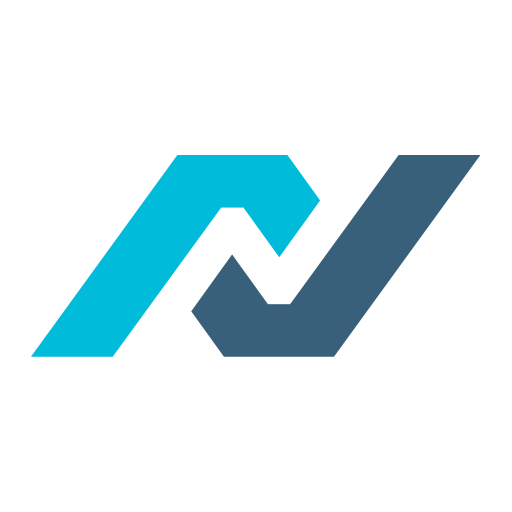
Northern Steel Ltd
9588 Milwaukee WayPrince George British Columbia V2N 5T3 CA
Northern Steel is a custom steel fabrication and machining manufacturer. We've been providing custom fabrication and machining services since 1977 to clients in the Oil & Gas, Mining, Chemical, Pulp & Paper and Energy sectors throughout Canada and globally. Our team consists of experienced, innovative and collaborative members and you could be the fit we are looking for.
Job Details
-
Location9588 Milwaukee Way Prince George British Columbia
-
TypeFull-Time
-
Wage$100000 - $125000 per Year
-
Hours40 Hours Per Week
-
Experience10 Years
-
Start DateDecember 17, 2024
-
Closing DateDecember 31, 2025
-
Posted4 months ago